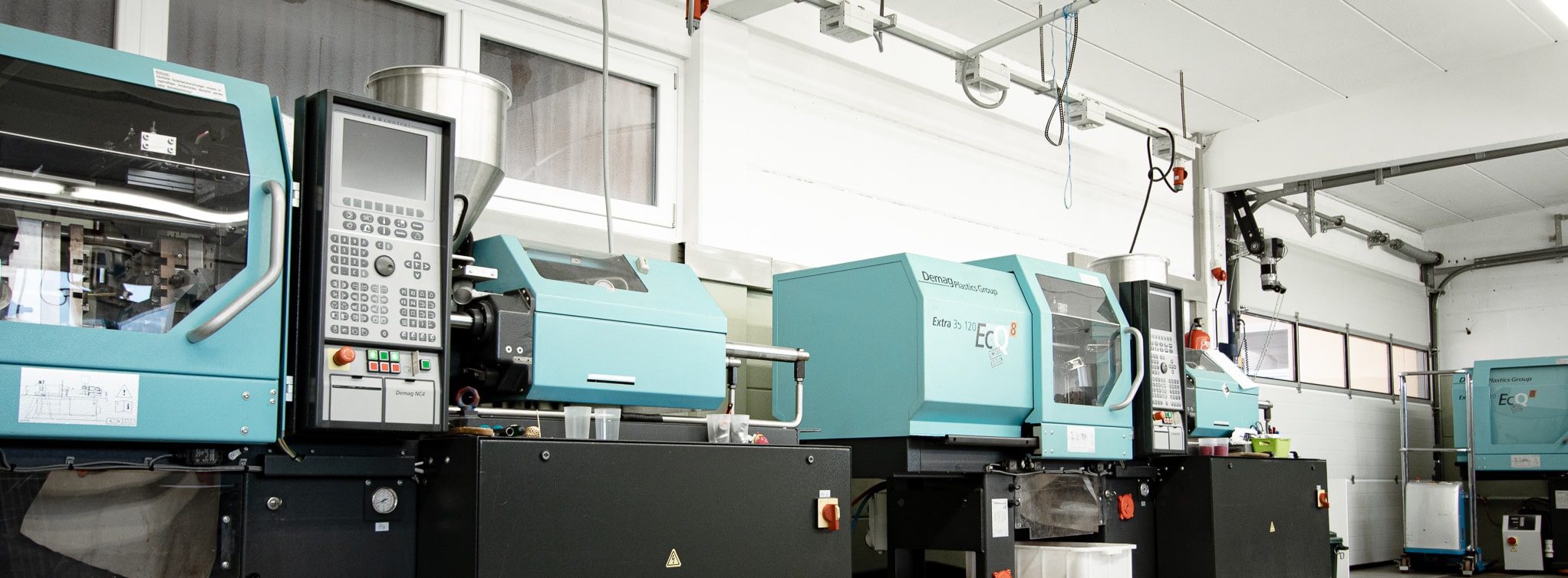
Spritzguss-Blog
-
Wie wird der Kunststoff verarbeitet?
Kunststoff entsteht aus Polymeren und wird durch Urformen, Umformen, Fügen und Veredeln zu vielseitigen Produkten für Alltag und Industrie verarbeitet.
-
Herstellung von Kunststoffen
Die Kunststoffe-Herstellung basiert meist auf Polymerisation aus Erdöl, während Biokunststoffe als nachhaltige Alternativen für die Zukunft gelten.
-
Hochleistungskunststoffe
Hochleistungskunststoffe zeichnen sich durch außergewöhnliche Hitzebeständigkeit, chemische Resistenz und mechanische Festigkeit aus.
-
Rezyklat
Rezyklat Als Rezyklat werden heute wiederaufbereitete Kunststoffabfälle bezeichnet, die als Sekundärrohstoffe in neuen Produktionsprozessen Verwendung finden. Der Einsatz von Rezyklaten hat nicht nur eine […]
-
PEEK – der Hochleistungskunststoff
PEEK – der Hochleistungskunststoff PEEK steht für Polyetheretherketon und ist ein vielseitig einsetzbarer, teilkristalliner Hochleistungskunststoff, der durch seine exzellente chemische Beständigkeit und hohe mechanische […]
-
Spritzgießen mit Polycarbonat
Polycarbonat Spritzgießen – Das Material ist aufgrund seiner hohen Festigkeit, Transparenz und Hitzebeständigkeit für viele Anwendungen geeignet!
-
PUR – Kunststoff der Spitzenklasse
Polyurethan ist unter dem Kürzel PUR bekannt. Der vielfältige, preiswerte Kunststoff wurde 1937 von Otto Bayer synthetisiert und gehört zur Urethan Gruppe.
-
Spritzgießen mit POM
Spritzgießen mit POM ist eine effiziente Technik für präzise Kunststoffteile. Hohe Festigkeit, Langlebigkeit und chemische Beständigkeit.
-
PTFE-Spritzgießen?
Das Spritzgießen mit PVC ist heute eine häufig verwendete Technik für die Herstellung von Armaturen und ähnlichen Bauteilen. Erfahren Sie hier mehr!
-
ABS Spritzgießen
Das Spritzgießen mit PVC ist heute eine häufig verwendete Technik für die Herstellung von Armaturen und ähnlichen Bauteilen. Erfahren Sie hier mehr!
-
Das Spritzgusswerkzeug
Als Spritzgusswerkzeug oder einfach Werkzeug wird beim Spritzguss die zweiteilige Hohlform oder Matrize bezeichnet, in die der flüssige Kunststoff eingefüllt wird.
-
Der 2K Spritzguss
Der 2K Spritzguss spielt einer sehr wichtige Rolle in der heutigen Wirtschaft. In diesem Spritzguss-Blog erfahren Sie mehr über das 2K Spritzgießen.