PUR – Kunststoff mit vielen Eigenschaften
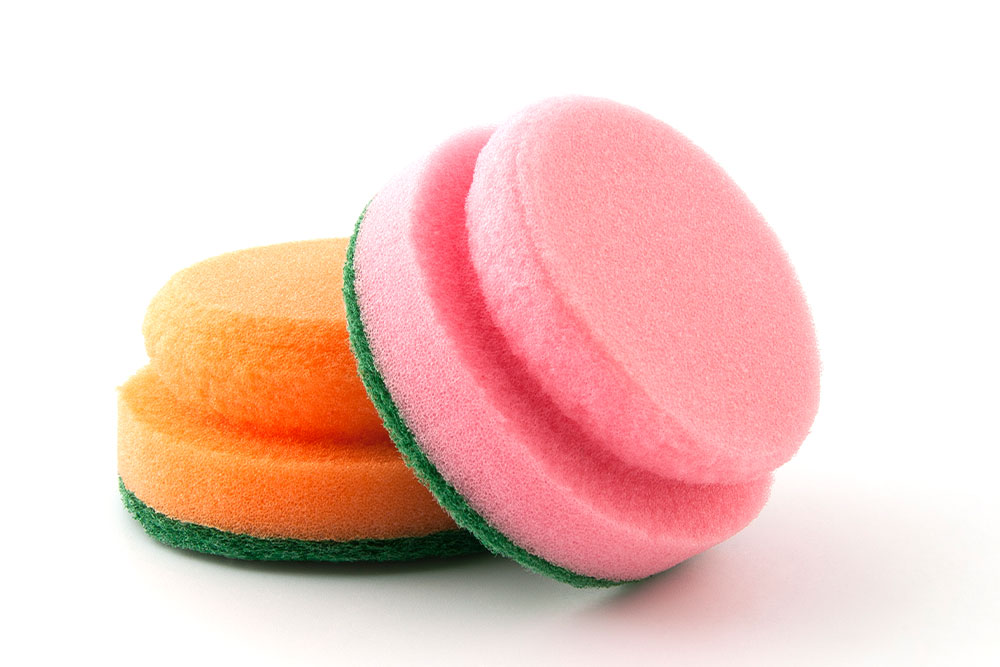
Polyurethan ist ein vielseitiger Kunststoff, der durch die Reaktion von Polyolen mit Isocyanaten entsteht. Er kann in verschiedenen Formen hergestellt werden, einschließlich Schäumen, Hartplasten und Beschichtungen. Polyurethan wird in zahlreichen Anwendungen verwendet, darunter in Polstermöbeln, Matratzen, Isolationsmaterialien, Farben und Lacken. Es ist flexibel, langlebig und widerstandsfähig gegen chemische und mechanische Einflüsse.
Inhaltsverzeichnis
Wir planen und produzieren auch für Ihre Branche und Ihr Unternehmen.
Senden Sie uns Ihre Anfrage oder rufen Sie einfach an,
wir sind gerne für Sie da.
Die Geschichte eines Alleskönners
Polyurethan ist in der Öffentlichkeit unter dem Kürzel PUR oder noch einfacher PU bekannt. Polyurethan ist ein vielfältigers und preiswertes Material, der 1937 von Otto Bayer synthetisiert wurde. Bayer war bei den Farbenfabriken BAYER in Leverkusen tätig und entwickelte Polyurethan durch die Umsetzung von 1,4-Butandiol mit Octan-1,8-diisocyanat. Die industrielle Produktion begann 1940, musste jedoch bald schon wegen des Rohstoffmangels unterbrochen werden. Trotzdem gelang es Otto Bayer, ein Verfahren zur Herstellung geschäumter Polyurethane zu entwickeln.
Nach dem Krieg wurden durch den Einsatz unterschiedlicher Ausgangsstoffe bald Polyurethan-Kunststoffe mit sehr unterschiedlichen Eigenschaften hergestellt. Diese maßgeschneiderten Kunststoffe begeisterten die Fachwelt mit ihren ganz unterschiedlichen Eigenschaften. Die Varianten reichten von hart und spröde über weich und elastisch bis hin zu dünnflüssig und hochviskos. Heute werden weltweit jährlich über 7 Mio. Tonnen Polyurethan hergestellt, 90% davon in Form von Schäumen.
Die chemische Zusammensetzung von PUR
Polyurethan-Kunststoffe bestehen aus Urethan-Gruppen und werden durch die Reaktion von mehrwertigen Alkoholen mit Polyisocyanaten mittels Polyaddition hergestellt. Bei diesem Prozess verbinden sich die Monomere ohne die Bildung von Nebenprodukten. Mehrwertige Alkohole sind organische Moleküle mit mindestens zwei Hydroxylgruppen (OH). Wenn sie zwei Hydroxylgruppen haben, werden sie Diolen genannt, bei drei Triolen und bei mehr als drei Polyolen. Polyisocyanate sind organische Moleküle mit mindestens zwei Isocyanat-Gruppen (-NCO).
Die chemische Beständigkeit eines Polyurethans hängt hauptsächlich vom verwendeten Polyol ab, während die physikalischen Eigenschaften sowohl vom Polyol als auch vom gewählten Diisocyanat (wie NDI, MDI, TDI) und den Zusatzstoffen bestimmt werden. Grundsätzlich gibt es zwei Haupttypen von Polyurethanen. Das sind solche auf Ester- und solche auf Ether-Basis. Polyurethane auf Ester-Basis zeichnen sich durch Eigenschaften wie Verschleißfestigkeit und hohe mechanische Festigkeit aus. Bei den Polyurethanen auf Ether Basis kommen noch eine Hydrolysebeständigkeit, eine Kaltflexibilität bis zu -50°C und die Mikrobenbeständigkeit hinzu.
Die Eigenschaften und die Herstellung von PUR
Polyurethan ist bekannt für seine vielfältigen Einsatzgebiete und praktisch unvergleichlichen Eigenschaften. Ganz nach der Methode der Erzeugung kann Polyurethan weich und elastisch oder hart und spröde sein. Unabhängig von der Elastizität und dem damit verbundenen Vernetzungsgrad der Moleküle zeigt Polyurethan hervorragende Eigenschaften. Dazu gehören die Beständigkeit gegen Feuchtigkeit, Lösungsmittel, Fette und Kohlenwasserstoffe sowie gegen die UV-Strahlung. PUR ist schall- und wärmedämmend sowie leicht und stabil. Polyurethan behält seine Eigenschaften auch bei größeren Temperaturunterschieden zwischen -50°C und 80°C und kurzzeitig sogar bis zu 120°C bei. Dazu kommen die hohe mechanische Festigkeit, eine extrem hohe Verschleißfestigkeit, die sehr hohe Schlagzähigkeit und die guten Dämpfungswerte.
Die verschiedenen Eigenschaften der Polyurethane werden hauptsächlich durch Änderungen an der Zusammensetzung der Polyol-Komponenten beeinflusst. Wasserzugabe bei der Synthese führt zur Schaumbildung. Durch die Reaktion von Wasser mit Isocyanat wird Kohlendioxid freigesetzt, das den Polyurethanschaum aufbläht und dabei Dichten zwischen ca. 30 kg/m³ für weichen Schaum und etwa 90 kg/m³ für harten Schaum erzeugt. Ohne Wasserzugabe liegt die Dichte von Polyurethan bei 1.000 bis 1.300 kg/m³.
Erscheinungsformen und Einsatzgebiete von PUR
Polyurethan tritt als Duroplast, Thermoplast oder Elastomer auf und wird zu einer Vielzahl von Produkten weiterverarbeitet. Seine besondere Haltbarkeit und Leichtigkeit sind genauso beim Hausbau wie bei der Automobilproduktion geschätzt. In der Industrie wird Polyurethan als Belag für Rutschen, Rollen oder Walzen und als Rostschutz verwendet. Im Haushalt findet es sich in Matratzen, Sesseln oder Schwämmen. Aufgrund seiner Biokompatibilität ist Polyurethan auch perfekt für Küchen- und Haushaltsartikel geeignet.
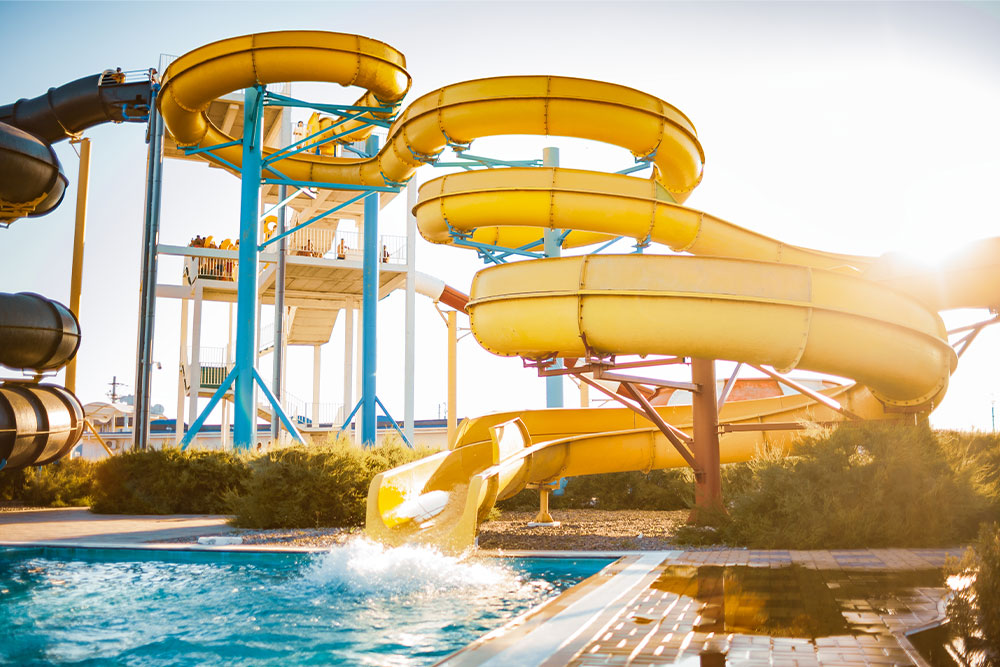
Weitere typische Produkte aus PUR
- Skischuhe mit einem Innenschuh aus PUR-Weichschaum und dem Außenbereich aus hartem, aber elastischem PUR. Diese Kombination verhält sich wasserdicht, kratzfest und elastisch auch bei niedrigen Temperaturen.
- Elastische Chemiefasern wie Elastan werden in Badebekleidung, Stretch-Jeans, Strumpfhosen und Miederwaren verwendet.
- Regenkleidung und Funktionsjacken profitieren von einer PU-Beschichtung, die Tragekomfort und Atmungsaktivität verbessert.
- Helme, Fahrradsättel, Snowboards, Rollschuhrollen, Fußbälle und selbst die äußere Schicht von Bowlingkugeln werden aus Polyurethan gefertigt.
In der Automobilindustrie finden sich Polyurethane in Armaturenbrettern, Türverkleidungen, Sitzen, Heckklappen und als Faservliese. Schläuche aus Polyurethan ersetzen dank ihrer hohen Verschleiß- und Reißfestigkeit sowie ihrer Beständigkeit gegenüber Ozon und Benzin immer häufiger Schläuche aus Gummi oder Naturkautschuk.
PU-Klebstoffe zeichnen sich durch hohe Witterungs- und Alterungsbeständigkeit sowie eine hohe Schlag- und Scherfestigkeit aus. Damit eignen sie sich bestens für großflächige Verklebungen verschiedener Oberflächen im Innen- und Außenbereich.
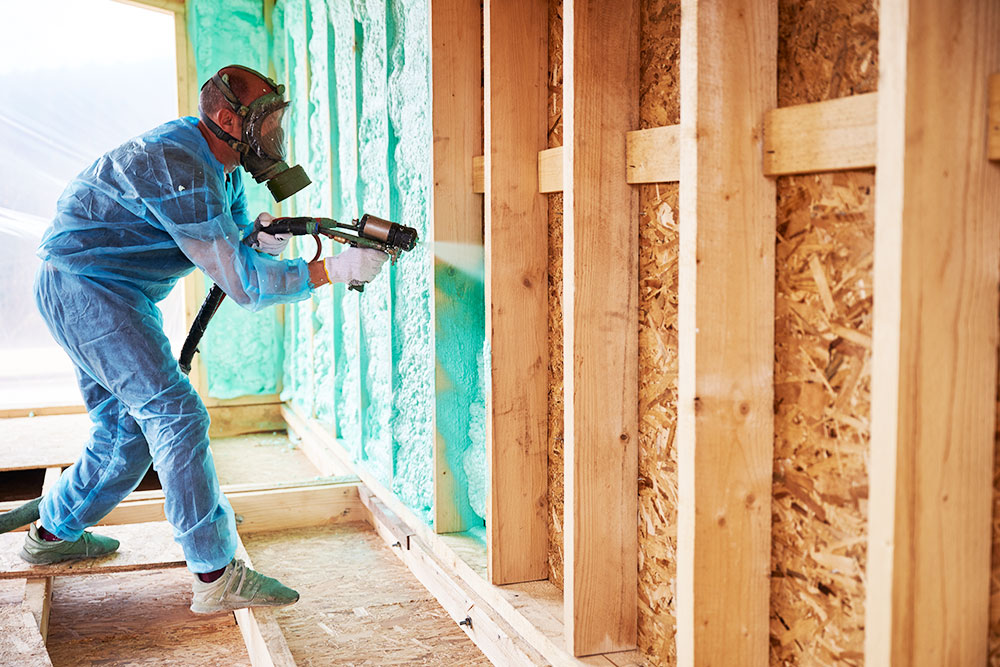
Die Verarbeitung von PUR als Bauteil
Das Spritzgießen der Polyurethane unterscheidet sich deutlich vom Spritzguss anderer Kunststoffe. Das Reaction Injection Moulding (RIM) Verfahren, bei dem die Komponenten während des Prozesses gemischt werden, ermöglicht die Herstellung von Bauteilen mit unterschiedlichen Formen und Materialeigenschaften.
Unterschiede zum normalen Kunststoff-Spritzguss
Die Reaktionsphase bei RIM dauert wenige Minuten, danach kann das Polyurethan-Bauteil ausgeworfen werden. Aufgrund der niedrigeren Viskosität der Reaktionsmasse sind höhere Abdichtungen und eine extrem genaue Dosierung erforderlich.
Der niedrige Pressdruck und die niedrigen Temperaturen beim RIM-Verfahren reduzieren die Kosten für die Werkzeug-Herstellung erheblich, da Materialien wie Aluminium oder Kunststoff verwendet werden können.
Kombination von Spritzguss und Reaction Injection Moulding
Eine weitere Methode kombiniert traditionellen Spritzguss mit RIM. Zunächst werden thermoplastische Elemente im Spritzguss hergestellt und anschließend mit einer PUR-Mischung geflutet. Dies erzeugt eine zusätzliche Schicht mit hoher Formgenauigkeit und überzeugender Haptik.
Wie lässt sich PUR recyceln?
Das Recycling von PUR stellt eine besondere Herausforderung dar, da Polyurethan, wie gesagt, in vielen verschiedenen Formen und Zusammensetzungen existiert. Die Recyclingfähigkeit von PUR-Typen variiert stark. Weiche PUR-Schäume sind leichter zu recyceln als harte PUR-Kunststoffe.
Mechanisches Recycling
Der mechanische Recyclingprozess ist die am häufigsten angewendete Methode. Jedoch ist hierfür ein sortenreines Sammeln empfehlenswert, da sonst die Qualität des Rezyklats sinkt. Die gesammelten Abfälle werden mechanisch zu kleineren Partikeln oder Pulver zermahlen. Die zerkleinerten Partikel werden zu Granulat verarbeitet, das dann als Rohmaterial für die Herstellung neuer PUR-Erzeugnisse verwendet werden kann. Dieses Granulat wird direkt in neue Fabrikate integriert oder als Füllmaterial eingesetzt.
Chemisches Recycling
Das chemische Recycling von PUR ist ein komplexer und derzeit noch teurer Prozess, der darauf abzielt, die chemischen Bestandteile des Materials wiederzugewinnen. Dies geschieht durch die sogenannte Glykolyse, Hydrolyse oder Pyrolyse. Bei der Glykolyse wird PUR in seine Grundbestandteile, Polyole und Diisocyanate zerlegt, indem es mit Glykolen unter erhöhter Temperatur und Druck reagiert. Diese Reaktionsprodukte werden dann zur Erzeugung neuer Polyurethane verwendet. Bei der Hydrolyse wird PUR unter stark erhöhter Temperatur und Druck mit Wasser behandelt und die Polymerketten in ihre Monomere zerlegt.
Diese Monomere werden gereinigt und wiederverwendet. Bei der sogenannten Pyrolyse wird PUR bei hohen Temperaturen unter Abwesenheit von Sauerstoff zersetzt. Dabei entstehen verschiedene Gase und Flüssigkeiten, die als chemische Rohstoffe weiterverarbeitet werden können. Oft bleibt aufgrund des Aufwands jedoch nur die energetische Verwertung durch die Verbrennung in speziellen Anlagen, um Energie in Form von Strom und Wärme zu gewinnen. Diese Methode zerstört allerdings die Materialressourcen und verursacht zusätzliche Emissionen.