PEEK – der Hochleistungskunststoff
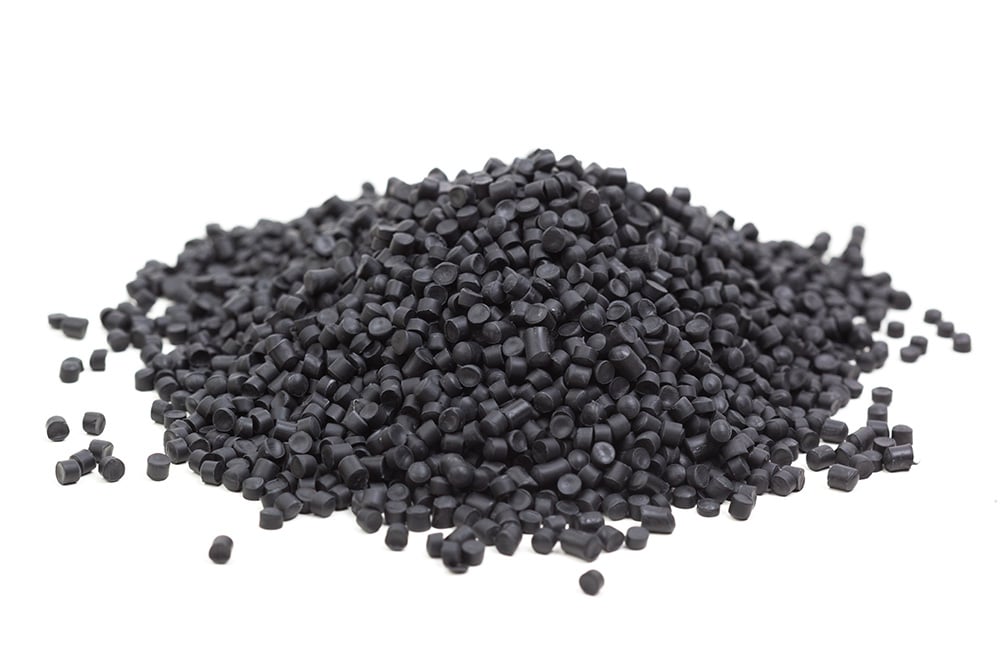
PEEK steht für Polyetheretherketon und ist ein vielseitig einsetzbarer, teilkristalliner Hochleistungskunststoff, der durch seine exzellente chemische Beständigkeit und hohe mechanische Festigkeit überzeugt. Dank der hohen Wärmeform- und Temperaturbeständigkeit können PEEK-Bauteile bei Temperaturen von bis zu 260 °C eingesetzt werden. Der Schmelzpunkt liegt bei etwa 340 °C. Hochleistungskunststoffe nehmen unter den Kunststoffen einen ganz besonderen Platz ein. Die Kombination aus hoher Leistungsfähigkeit und spezifischen Merkmalen wird für viele anspruchsvolle Anwendungen benötigt, die dann sogar einen hohen Preis für die Herstellung rechtfertigen. Der folgende Artikel behandelt das Material PEEK (Polyetheretherketon), von seinen Eigenschaften über die Anwendungsen, die Herstellungsprozesse bis hin zu den Kosten und der Wiederverwertung.
Wir planen und produzieren auch für Ihre Branche und Ihr Unternehmen.
Senden Sie uns Ihre Anfrage oder rufen Sie einfach an,
wir sind gerne für Sie da.
Was sind Hochleistungskunststoffe?
Hochleistungskunststoffe bilden eine spezielle Kategorie der Kunststoffe, die sich durch ihre außergewöhnlichen chemischen, thermischen und mechanischen Eigenschaften auszeichnen. Diese Materialien halten extremen Bedingungen wie hohen Temperaturen, aggressiven Chemikalien, hohem Druck und starker mechanischer Belastung stand, ohne dabei ihre strukturelle Integrität bzw. Leistungsfähigkeit zu verlieren. Hochleistungskunststoffe werden häufig in anspruchsvollen technischen Anwendungen eingesetzt, wo herkömmliche Kunststoffe an ihre Grenzen stoßen. Man findet sie als Werkstoff etwa in der Luft- und Raumfahrt, in der Automobilindustrie, in der Medizintechnik und in der Elektronik. Beispiele für Hochleistungskunststoffe sind PEEK, PTFE, Polyimid und Polyetherimid (PEI).
PEEK und seine Eigenschaften
Polyetheretherketon oder auch Polyether-Etherketon ist ein hochtemperaturbeständiger thermoplastischer Kunststoff und gehört zur Gruppe der Polyaryletherketone. Seine Schmelztemperatur beträgt etwa 340 °C. PEEK ist als Werkstoff bekannt für seine außergewöhnlich hohe mechanische Festigkeit und chemische Beständigkeit gegen die meisten aggressiven Verbindungen. Es kann kontinuierlich bei Temperaturen von bis zu 260°C eingesetzt werden, ohne dass seine Eigenschaften darunter leiden. Das übersteigt z.B. die Beständigkeit von POM (Polyoxymethylen) bei weitem. PEEK bietet gute Isoliereigenschaften sowie eine hohe Verschleißfestigkeit. Seine Stabilität und Resistenz gegenüber aggressiven Substanzen machen das PEEK zu einem begehrten Material in anspruchsvollen Anwendungsbereichen. Im festen Zustand lässt sich das PEEK drehen, sägen, bohren, hobeln oder fräsen. Im geschmolzenen Zustand kann es im Spritzguss oder mit der Extrusion geformt werden. Dazu kommt das geringe Gewicht des PEEK. Diese Kombination verleiht PEEK einen besonderen Status. Allerdings zeigt das PEEK auch Schwächen. Es verhält sich unbeständig gegenüber UV-Strahlung in Verbindung mit Luftsauerstoff und reagiert empfindlich auf konzentrierte Salpetersäure.
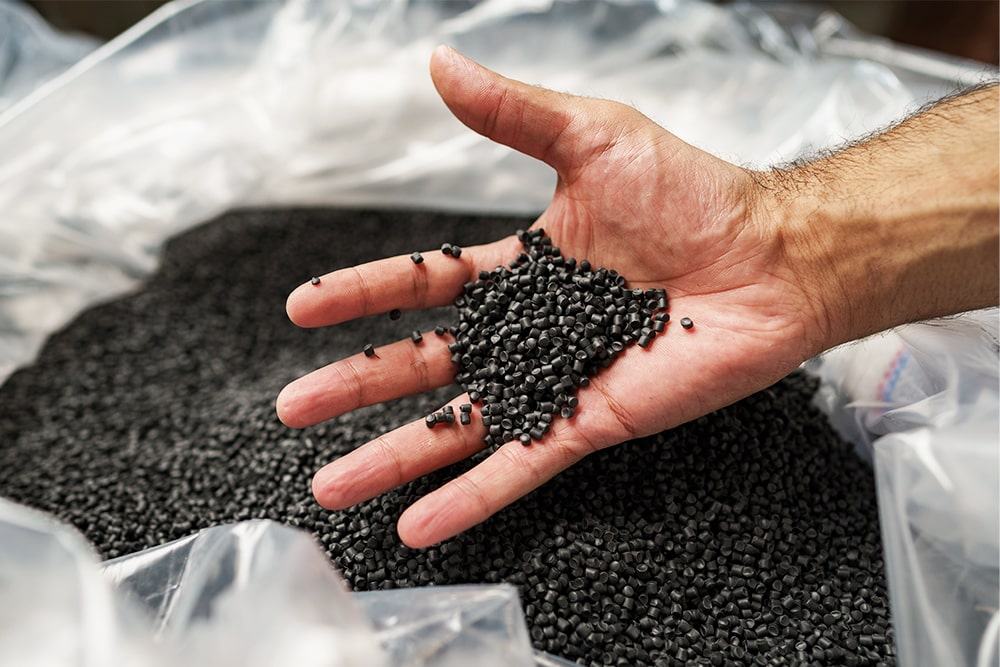
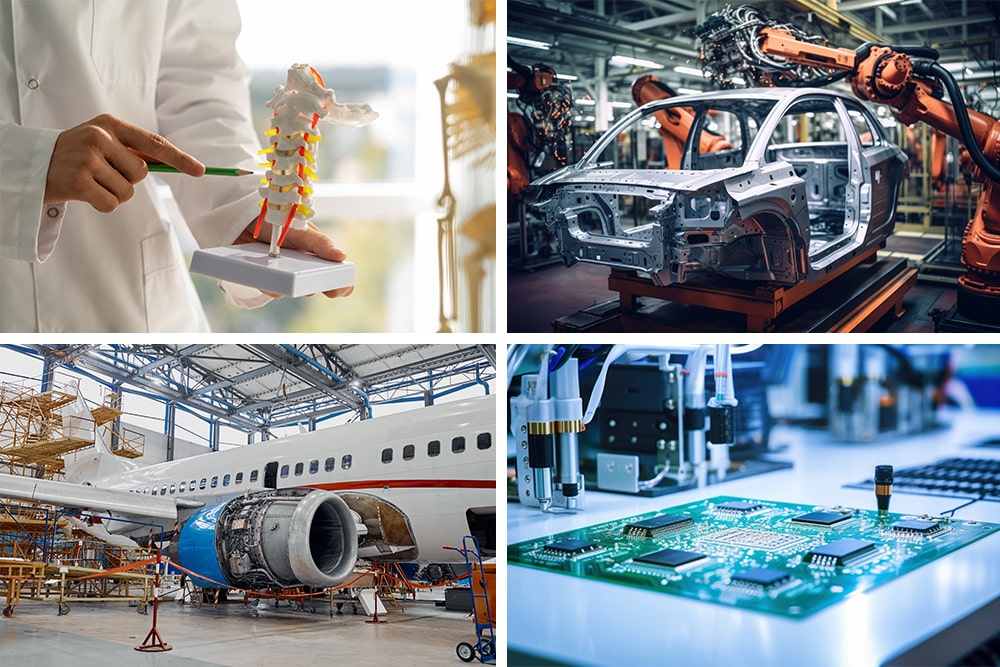
Hier die Darstellung der Eigenschaften von PEEK als Liste
- PEEK kann kontinuierlich bei Temperaturen von bis zu 260°C eingesetzt werden.
- PEEK hat eine sehr geringe thermische Ausdehnung, was zu hoher Dimensionsstabilität führt. PEEK behält seine Form auch bei Temperaturschwankungen sehr gut.
- Gute mechanische Festigkeit, Steifigkeit und Kriechfestigkeit auch bei hohen Temperaturen.
- Herausragende chemische Hydrolysebeständigkeit.
- PEEK ist sehr abriebfest und eignet sich daher für Anwendungen mit hohen mechanischen Belastungen.
- PEEK hat eine geringe Reibung und ist daher gut für bewegliche Teile geeignet.
- PEEK lässt sich zur elektrischen Isolation verwenden.
- PEEK ist resistent gegen eine Vielzahl von Chemikalien, einschließlich schwacher Säuren, Laugen und Lösungsmitteln.
- PEEK ist beständig gegen heißes Wasser und Dampf.
- PEEK ist resistent gegen ionisierende Strahlung.
- Der Werkstoff entwickelt im Brandfall nur wenig Rauch.
- Bestimmte Sorten von PEEK sind biokompatibel und finden Anwendung in der Medizintechnik.
Anwendungsbereiche von PEEK
PEEK-Kunststoffe finden Verwendung in einer Vielzahl von Branchen, darunter die Luft- und Raumfahrt, die Automobilindustrie, Medizintechnik und Elektronik. Es wird für Komponenten verwendet, die hohe Anforderungen an die Materialbeständigkeit stellen, wie z.B. Implantate, Isolatoren oder Bauteile in der Automobil- und Flugzeugkonstruktion. In der Luft- und Raumfahrtindustrie dient es als Komponente für hochbelastete Teile, die Leichtigkeit mit Stabilität vereinen müssen. Im Automobilsektor ermöglicht das PEEK neue Entwicklungen im Leichtbau und in der Leistungssteigerung. Auch in der Medizintechnik hat PEEK aufgrund seiner guten Biokompatibilität und Sterilisierbarkeit einen festen Platz. In der Elektronikindustrie schützt es sensible Bauteile vor thermischen und chemischen Einflüssen. Diese branchenübergreifende Präsenz unterstreicht die Bedeutung des Polyetheretherketon und erklärt seinen hohen Bekanntheitsgrad.
Der Herstellungsprozess von Polyetheretherketon
Der Herstellungsprozess von Polyetheretherketon in seinen verschiedenen Erscheinungsformen besteht aus einer ganzen Reihe von Schritten einer komplexen chemischen Synthese.
Ausgangsmaterialien und Polymerisation
Die genaue Zusammensetzung der Ausgangsstoffe für die Herstellung von PEEK kann je nach Hersteller und gewünschter Eigenschaft des Endprodukts variieren. Grundsätzlich werden jedoch folgende Monomere als Ausgangsstoffe für PEEK-Kunststoffe eingesetzt:
- Bisphenol A:
Dieses Diphenol ist ein wichtiger Baustein für viele Kunststoffe und dient als Verbindungselement zwischen den Ether-Einheiten in der PEEK-Kette. - 4,4′-Difluorbenzophenon:
Dieses aromatische Dihalogenid ist für die Bildung der Etherbindungen zwischen den Bisphenol-A-Einheiten verantwortlich.
Die Monomere werden in einem kontrollierten Umfeld zusammengeführt, um die Polymerisation einzuleiten. Diese Reaktion erfolgt typischerweise in einem Lösungsmittel unter Anwendung von Hitze und Druck. Damit wird die Bildung von langen Ketten aus Ether- und Ketogruppen ermöglicht, die für das PEEK charakteristisch sind. Die Ether- und Ketogruppen werden über aromatische Arylgruppen verbunden. Die Ether- und Ketogruppen können dabei nahezu beliebig angeordnet sein, was zu einer großen Bandbreite von steuerbaren Materialeigenschaften führt.
Hochtemperatur-Polykondensation
Nach der initialen Polymerisation durchläuft das entstehende Polymer eine Polykondensation bei extrem hohen Temperaturen. So lässt sich ein Polymer mit hohem Molekulargewicht erreichen, das für die mechanischen und thermischen Fähigkeiten von PEEK verantwortlich ist. Die Polykondensation erfordert die präzise Überwachung der Temperatur, damit die gewünschte Polymerstruktur ohne Abbau der Ketten zu erreichen ist.
Isolierung und Reinigung
Nachdem das PEEK-Polymer gebildet wurde, muss es von Lösungsmitteln und anderen Nebenprodukten getrennt werden. Dazu setzt man verschiedene Verfahren wie Ausfällung, Filtration und Trocknung ein. Diese Reinigung ist ein wesentliches Element des Prozesses, mit dem die Reinheit des Endprodukts erreicht wird.
Formgebung
Das gereinigte PEEK-Polymer wird anschließend in die gewünschte Form gebracht. Dies kann durch Extrusion, Spritzgießen oder das Pressen von Pulver zu Halbzeugen erfolgen. Die spezifische Methode hängt von der endgültigen Anwendung des Materials ab. Die hohe Schmelztemperatur von 335° Celsius stellt extreme Anforderungen an eine spezielle Ausrüstung und Technik der kunststoffverarbeitenden Unternehmen. Das trägt zu den hohen Kosten der Herstellung bei.
Nachbearbeitung
In vielen Fällen wird das Material nach der Formgebung einer Nachbearbeitung unterzogen, um spezifische Oberflächeneigenschaften herzustellen. Dies umfasst z.B. mechanische Bearbeitung, Polieren oder Beschichten. Die Nachbearbeitung ist Voraussetzung für Anwendungen mit hoher Präzision und Oberflächenqualität, wie sie typisch für die Medizintechnik oder die Luft- und Raumfahrt sind.
Kosten und Wiederverwertung: Lohnt sich die Investition?
Die Frage nach der Wirtschaftlichkeit von PEEK lässt sich nicht allein durch den Preis pro Kilogramm beantworten. Zwar übersteigen die Anschaffungskosten dieser Arten Kunststoffe leicht das Zehnfache von herkömmlichen Materialien, aber das zahlt sich je nach Anwendungsbereich aus. Die hohe Verschleißfestigkeit und Lebensdauer des Werkstoffs sorgt dafür, dass ein Austausch eines Bauteils seltener erfolgen muss. Das führt gleichzeitig zu geringeren Lebenszykluskosten der Anlagen. Die Maschinen, in denen Teile aus PEEK verbaut sind, verfügen oft über längere Laufzeiten und benötigen weniger Reparaturen.
PEEK wird trotz einiger Herausforderungen des Prozesses zunehmend recycelt
Beim mechanischen Recycling werden gebrauchte PEEK-Produkte zerkleinert, aufgeschmolzen und zu neuen Produkten verarbeitet. Aufgrund der hohen Temperaturbeständigkeit und der Beständigkeit gegen chemische Abbauprozesse behält das Material auch nach dem Recycling viele seiner hervorragenden Materialeigenschaften bei. Das chemische Recycling geht noch einen Schritt weiter: Hierbei wird PEEK in seine Grundbestandteile zerlegt, die dann wieder zur Synthese neuen PEEKs verwendet werden können. Dieses Verfahren ist jedoch auch gerade wegen der Beständigkeit des PEEK sehr aufwändig. Die Herausforderungen liegen vor allem in der Vermeidung von Verunreinigungen, die die Qualität des recycelten Materials beeinträchtigen können. Auch die Kosten für die Einrichtung und den Betrieb solcher Recyclinganlagen sind nicht zu unterschätzen.